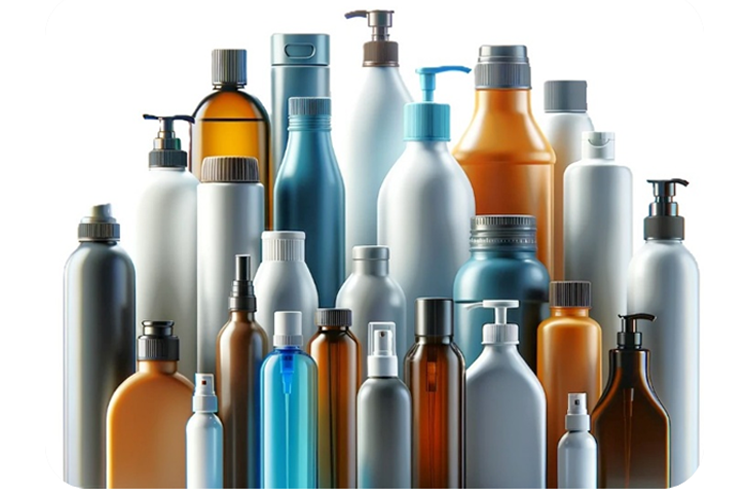
The Future of Capping Machines – Why Flexibility is Key
The bottling and packaging industry is evolving rapidly, with contract manufacturers facing increasing demands for higher efficiency, faster changeovers, and greater adaptability. With a growing range of product SKUs, packaging formats, and regulatory requirements, flexible capping machines have become essential for businesses looking to stay ahead.
At Process Evolution, we design and build advanced capping machines in Australia, tailored to meet the diverse needs of contract manufacturers. Our solutions are engineered for efficiency, reliability, and adaptability, ensuring seamless production across multiple bottle and cap formats.
In this article, we explore the future of capping machines, why flexibility is key, and how Process Evolution is leading the way with Australian-made automation solutions.
How Capping Machines Are Evolving in Modern Manufacturing
The Shift Towards Greater Automation and Efficiency
As global demand for faster, more efficient production lines continues to grow, manufacturers are shifting towards fully automated capping solutions. Today’s capping machines integrate servo-driven torque control, AI-driven quality checks, and rapid changeover capabilities to ensure higher precision and consistency.
Key advancements include:
✔ Automated torque control for consistent and secure sealing
✔ Vision inspection systems to detect capping errors in real time
✔ High-speed automation that minimises bottlenecks in production
Why Flexibility is Crucial in Today’s Production Lines
With consumer preferences shifting rapidly, manufacturers must be able to adapt to new product formats quickly. A flexible capping machine allows businesses to:
✔ Handle multiple cap types (e.g., screw caps, flip-top caps, pumps etc.)
✔ Accommodate various bottle sizes and shapes
✔ Reduce downtime with quick and easy changeovers
By investing in a flexible solution, contract manufacturers can future-proof their production lines and keep up with market demands without requiring frequent equipment upgrades.
The Role of Flexible Capping Machines in Contract Manufacturing
Adapting to a Diverse Range of Bottles and Caps
For contract manufacturers, working with multiple clients and product types means production lines must be capable of handling a wide variety of bottles and caps.
A flexible capping machine ensures:
✔ Seamless transitions between different cap and bottle formats
✔ Minimal manual adjustments, reducing labour costs
✔ Precision capping across various container materials, including plastic, glass, and aluminium
Quick Changeovers for Multi-SKU Production
Time is money in manufacturing, and long changeover times between production runs can slow down operations and increase costs.
Our flexible capping machines are designed with:
✔ Tool-free adjustments for rapid SKU changes
✔ Servo-driven cap sorting and application
✔ User-friendly interfaces to streamline setup
This allows manufacturers to switch from one product line to another quickly, ensuring maximum efficiency and profitability.
Reducing Downtime and Increasing Output
Unplanned downtime is one of the biggest challenges in manufacturing. A locally designed and built capping machine from Process Evolution provides:
✔ Robust, durable construction for 24/7 operation
✔ Locally sourced spare parts for faster repairs
✔ Immediate technical support from our Australian engineering team
This ensures higher machine availability and increased production output for contract manufacturers.
Process Evolution – Leading the Way in Australian-Made Capping Machines
Locally Designed and Built for Australian Manufacturers
Unlike imported machines that may not meet local industry standards, Process Evolution provides Australian-made capping machines designed specifically for Australian contract manufacturers.
Engineering Expertise and In-House Support
By choosing Process Evolution, you benefit from:
✔ Direct access to local engineers and technicians
✔ On-site support for commissioning and maintenance
✔ Faster response times for troubleshooting and repairs
Faster Lead Times with Locally Sourced Components
With global supply chain disruptions affecting manufacturing, sourcing equipment locally ensures:
✔ Faster delivery times compared to overseas imports
✔ Reliable access to spare parts and upgrades
✔ Ongoing technical support from our Australian team
Key Features of Next-Generation Capping Machines
Servo-Driven Torque Control for Precision Capping
Advanced servo-driven technology ensures:
✔ Consistent torque application for leak-proof sealing
✔ Reduced wear and tear, extending machine lifespan
✔ Real-time torque adjustments for different cap types
Smart Automation and Industry 4.0 Integration
Modern capping machines are incorporating Industry 4.0 technologies, such as:
✔ AI-powered quality control to detect faulty seals
✔ Cloud-based monitoring for real-time performance tracking
✔ Data-driven analytics to optimise production efficiency
Customisation for Specific Product and Industry Needs
Every manufacturer has unique requirements, which is why we offer custom-built capping solutions that integrate seamlessly into your existing production line.
The Benefits of Choosing an Australian-Made Capping Machine
Compliance with Australian Manufacturing Standards
Our capping machines meet all Australian safety and quality standards, ensuring regulatory compliance across multiple industries.
Lower Maintenance Costs with Local Parts and Service
With local service and spare parts availability, manufacturers benefit from:
✔ Lower operational costs
✔ Reduced downtime
✔ Immediate technical support
Supporting Australian Innovation and Industry Growth
By investing in Australian-made machinery, businesses help:
✔ Strengthen the local economy
✔ Support local engineering expertise
✔ Ensure long-term innovation in the manufacturing sector
Future Trends in Capping Machine Technology
The Rise of AI and Machine Learning in Capping Automation
AI-powered predictive maintenance is reducing machine failures by detecting faults before they occur.
Sustainability and Energy-Efficient Capping Machines
Energy-efficient designs are helping manufacturers lower electricity consumption and reduce carbon footprints.
The Role of Robotics in Fully Automated Packaging Lines
Robotic pick-and-place systems and automated cap feeding are driving fully integrated capping solutions for high-speed production lines.
Invest in a Future-Ready Capping Machine with Process Evolution
Talk to Our Experts About Custom Solutions
Looking for a high-performance capping machine built for Australian manufacturers? Process Evolution provides custom, flexible solutions tailored to your production needs.
Final Thoughts
The future of capping machines is flexible, automated, and highly efficient. With Process Evolution, Australian manufacturers gain locally designed, high-performance solutions that reduce downtime, increase output, and support long-term growth.
Contact us today to discover how our Australian-made capping machines can optimise your production line.